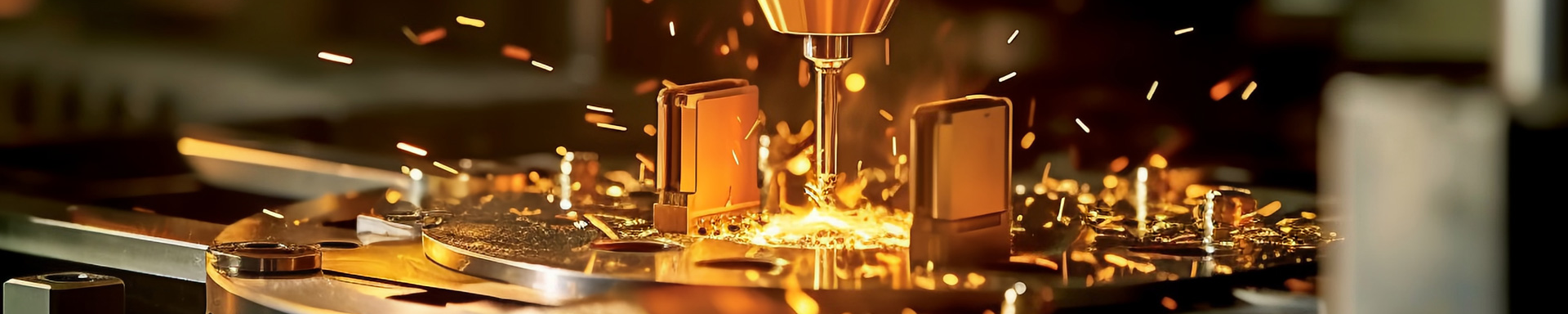
SMC Insert Mould Solutions for High-Performance Thermosetting Components
2025-07-09 14:33SMC Insert Mould Solutions for High-Performance Thermosetting Components
Precision BMC and Bakelite Molding for Electrical Applications
Material Expertise
Our SMC insert mould and BMC molding processes specialize in manufacturing durable electrical components like switches and iron housings. The thermosetting material properties require:
Mold temperatures of 150-180°C for optimal cure
High-pressure resistance (80-120 MPa)
Precision cavity/core steel (H13) for extended tool life
Tooling Specifications
Parameter | Specification |
---|---|
Mold Type | Thermoset Mold |
Base Material | LKM Standard |
Gating System | Cold runner, edge gate |
Dimensional Tol. | ±0.2mm |
Surface Finish | SPI-A2 (500+ cycles) |
Key Advantages of BMC and Bakelite Molding
Insert Molding Capability
Seamless integration of metal contacts in SMC insert mould designs
Reduced secondary operations for electrical assemblies
Thermal Performance
Bakelite components withstand 200°C continuous service
UL94 V-0 flame resistance in all thermosetting material outputs
Production Efficiency
Fast cure cycles (45-90 seconds) vs. thermoplastics
Minimal flash with precision mold insert alignment
Electrical Industry Applications
Circuit breaker housings (BMC)
High-temp appliance bases (Bakelite)
Arc-resistant switchgear (SMC insert mould)
Technical Innovation
Our latest mold insert technologies address:
Automated degating systems for thermoset runners
Conformal heating channels for even cure
Interchangeable inserts for multi-cavity BMC tools
Quality Assurance
All thermosetting material components undergo:
Dielectric strength testing (15kV/mm)
Thermal cycling validation (-40°C to 180°C)
Comparative tracking index (CTI >600V)
Why Choose Our Thermoset Molding?
15+ years in SMC/BMC mold manufacturing
Full DFM support for Bakelite components
Certified IATF 16949 for automotive electricals